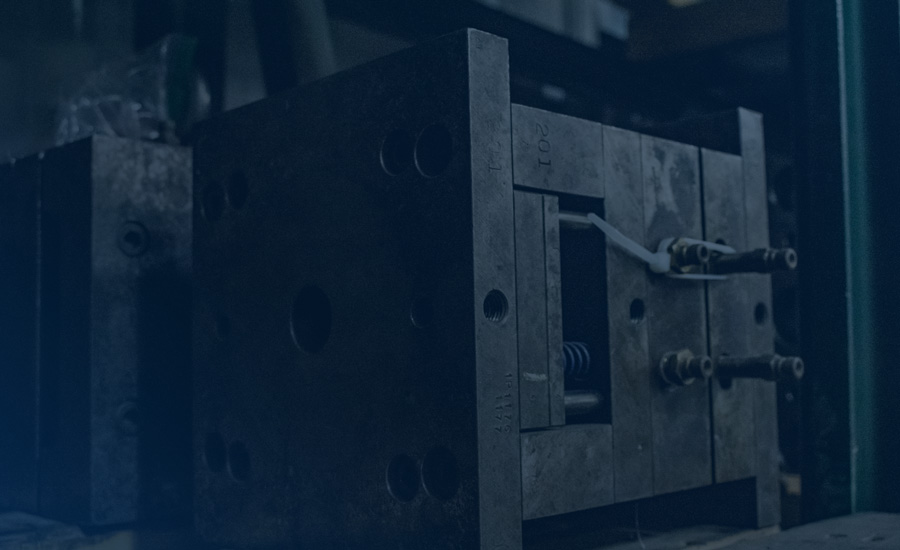
Tooling Capabilities
At NZK Plastics, we understand the importance of precision and cost-efficiency in tooling. Our expertise extends to both single and multi-cavity tools, family tools, insert molding, overmolding, and flex tooling for multiple part configurations. One of our standout capabilities is our ability to offer significant cost savings on tooling. By leveraging our long-standing partnerships with both foreign and domestic tooling suppliers, we bring the best of both worlds to our clients. Our collaboration with a select group of foreign tooling suppliers spans over two decades, and this trusted relationship has enabled us to save our customers thousands of dollars on tooling costs over the years.
Learn More About Our Tooling Capabilities
• Single and Multi-Cavity Tools:
Ideal for both low and high-volume production runs, our single and multi-cavity tools are meticulously designed to offer flexibility and cost-efficiency. Each tool is crafted to ensure consistent and precise molding, regardless of the production scale.
• Family Tools:
Streamline your production process with our family tools. By molding multiple parts of the same material simultaneously, we optimize production time and reduce costs. This approach ensures that all parts in a family mold maintain consistent quality and finish.
• Insert Molding:
Elevate the functionality of your products with our insert molding capabilities. This process integrates metal or other components directly into the plastic, creating a unified, durable product. It’s an ideal solution for enhancing the structural integrity and versatility of molded parts.
• OverMolding:
Enhance the aesthetics and performance of your products with our overmolding services. By adding an additional layer of material over your molded parts, we provide improved texture, grip, or added functionality, ensuring a premium finish.
• Flex Tooling / Multiple Part Configurations:
In the dynamic world of manufacturing, adaptability is key. Our flex tooling options are designed to accommodate changes with ease. Whether you need modifications or multiple part configurations, our flexible tooling ensures that you don’t need separate tools for each variation.
With NZK Plastics as your tooling partner, you can be confident in the precision, quality, and efficiency of every molded part. Our commitment to excellence, combined with our advanced tooling capabilities, sets the foundation for successful injection molding projects.



HAVE A QUESTION?
Send us a message.
TESTIMONIALS
What Our Clients Are Saying
NZK Plastics, LLC has been our go-to injection molding partner for years. Their attention to detail and commitment to quality is unparalleled. Highly recommended!
John D. Automotive Industry
We've worked with NZK Plastics on several critical projects, and they've always delivered on time and within budget. Their engineering services are top-notch, helping us optimize our designs for better
Sarah L. Medical Devices Manufacturer
NZK Plastics is incredibly responsive and knowledgeable. They helped us navigate material selection and even suggested design modifications that saved us money.
Mike H. Consumer Electronics
Sustainability is a big focus for us, and NZK Plastics was more than accommodating. They helped us select eco-friendly materials without compromising on quality. Truly a forward-thinking company!
Karen S. Renewable Energy Industry
We specialize in custom injection molding, part design and modification, tool development, process optimization, and rapid prototyping. Our engineering solutions are comprehensive and tailored to meet your specific needs.
We have been in the plastics industry for over 20 years, providing top-quality injection molding solutions to a diverse range of clients.
We work with a wide range of materials, including commodity resins like PE, PP, PS, ABS, PC, and Acetal, as well as high-end engineering resins like LCP, PPS, and COP.
Yes, we offer a variety of engineering services including SolidWorks CAD design, part design and modification, tool development, and process optimization.
Lead times can vary depending on the complexity of the project and the materials used. Please contact us for a more specific timeline.
Yes, we are equipped to handle both small and large production runs, thanks to our versatile injection molding machines ranging from 50 to 400 tons.
Quality assurance is built into every aspect of our manufacturing process. We adhere to strict quality control measures, including visual inspection, lot creation, data collection, and accurate measurements of product dimensions.
You can request a quote by contacting us through our website's contact form, or by calling or emailing us directly.
To provide an accurate quote, we typically need details like part design, material specifications, production volume, and any secondary operations or special requirements.